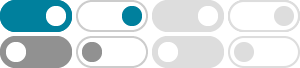
Toyota Business Practice (TBP) - Lean Manufacturing and Six …
The 8 steps are as follows: Clarify the problem; Breakdown the problem; Set a target; Analyze the root cause; Develop countermeasures; See countermeasures through; Evaluate both results and process; Standardize successful processes
TBP: Toyota Business Practice - Gemba Academy
Feb 22, 2009 · In this blog post, we explore the Toyota Business Practice (TBP) and its relationship with PDCA and A3 thinking. We also take a closer look at the 8 steps of TBP and how they can be mapped to an A3 document. Additionally, we discuss the problem-solving funnel and offer a deeper understanding of the 8 steps of TBP as written in Japanese.
8-Step A3 Practical Problem Solving Methodology - Belt Course
Oct 31, 2023 · The 8-Step Practical Problem Solving Process: The eight steps: Clarifying the problem and describing the current situation. Breaking down a big problem into smaller, more specific problems and studying the process. Setting a …
Using A3 Problem Solving to Make the Thinking Process Visible
Jan 26, 2012 · TBP is an eight-step process based on the Plan–Do–Check–Act cycle of quality guru J. Edwards Deming. In summary, the process begins with a statement of the problem, including the gap between the actual and the ideal condition.
Feb 8, 2020 · strengthen problem solving skills is called the 8-Step Problem Solving Process, some know it as TBP or Toyota Business Practices. (abbreviated):Outline Step 1 – Clarify the Problem (framing) Step 2 – Breakdown the Problem Step 3 – Target Setting Step 4 – Root Cause Analysis Step 5 – Develop Countermeasures
Toyota-style Problem Solving, Step 7: Check Both ... - Gemba Academy
Sep 21, 2009 · The eight step description of the PDCA cycle of problem solving called Toyota Business Practice (TBP for short) or practical problem solving continues to top my list of important things everyone should know. I’m finding it surprisingly hard to get people excited about this.
Toyota Business Practice - English.ppt - SlideShare
Jan 9, 2023 · The TBP utilizes a PDCA (Plan, Do, Check, Act) cycle and eight steps: 1) clarify the problem, 2) break down the problem, 3) set targets, 4) analyze root causes, 5) develop countermeasures, 6) implement countermeasures, 7) monitor results and processes, and 8) standardize successful processes.
Problem Solving Through Toyota Lean Management
Jun 10, 2021 · Consider these eight steps as you start on the path to continuous improvement. 1. Clarify the problem. The first step in solving a problem is realizing that one exists. You can define a problem by asking yourself the following questions: Does …
TOYOTA BUSINESS PRACTICES Overview - SlideServe
Nov 18, 2014 · Overall Image of TBP P D C A • TBP consists of: • 8 Steps (Concrete Actions & Processes) • Drive & Dedication Drive & Dedication Concrete Actions & Processes 1. Clarify the Problem 2. Break Down the Problem 3. Set a Target 4. Analyze the Root Cause 5. Develop Countermeasures 6. See Countermeasures Through 7. Evaluate Both Results and Processes 8.
Apply Toyota Business Practice (TBP)on new services
Nov 29, 2019 · To set a target and design the system to evaluate the effort is relatively important in the whole TBP cycle. A target drives people forward and an evaluation system tunes the method we use to...