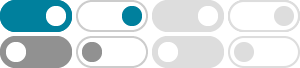
Who Was Shigeo Shingo and Why Is He Important to Process Improvement?
Nov 20, 2018 · A leader in the fields of continuous process improvement and operational excellence, Shigeo Shingo taught thousands of engineers at Toyota the Toyota Production System, influenced the creation of Kaizen and developed the concept of the Single-Minute Exchange of Die (SMED).
Shigeo Shingo - Lean Manufacturing and Six Sigma Definitions
Shigeo Shingō (1909-1990) was a Japanese industrial engineer who was heavily involved in the development and promotion of the Toyota Production System (TPS) to the rest of the world, specifically tools such as SMED, Poka-Yoke and Zero Quality Control (ZQC).
Shingo Model - Shingo Institute - Home of the Shingo Prize
In conjunction with the six Shingo workshop series, the Shingo Institute has published a series of books focused on the primary elements of the Shingo Model and its guiding principles.
Shingo, Shigeo (1909 - 1990) - Lean Enterprise Institute
2 days ago · Shingo, Shigeo (1909 – 1990) An engineer and consultant whose books and teaching made key contributions to the dissemination of the Toyota Production System. Shingo taught industrial engineering methods aimed at plant supervisors and engineers at Toyota from roughly 1955 to 1980.
Shigeo Shingo: Poka Yoke and SMED - Learn Lean Sigma
Shigeo Shingo revolutionized manufacturing with Poka-Yoke (mistake-proofing) and Single-Minute Exchange of Die (SMED), enhancing efficiency and quality in the Toyota Production System.
Shigeo Shingo and the Importance of Operational Excellence
Jan 24, 2022 · Shingo’s ten guiding principles are the building blocks of excellence and creating a sustainable working culture. Divided into four categories, the principles focus on culture development, improvement, an emphasis on understanding the company’s purpose, and the results of all their hard work.
Key people in the history of lean Six Sigma - 6Sigma Toolkit
Shigeo Shingo. A contemporary of Ohno, Shigeo Shingo contributed significantly to the development of the Toyota Production System. He is known for introducing the concepts of poka-yoke (mistake-proofing) and SMED (Single-Minute Exchange of Dies). Shingo's work on reducing errors and improving process setups blended seamlessly into the Lean ...
Lean Six Sigma Glossary Term - SMED - Sixsigma DSI
SMED (or Single Minute Exchange of Dies) is a method of reducing the time it takes to changeover (or set up) a machine. It involves identifying elements that are internal or external to the machine’s operation time, then converting those elements to externally while the machine continues to run.
OPS CHAPTER 12 Flashcards - Quizlet
Study with Quizlet and memorize flashcards containing terms like Which of the following are key aspects of the Shingo system?, What is required to prevent errors becoming defects?, What is the purpose of single-minute exchange of die (SMED) procedures in the Shingo System? and more.
Shigeo Shingo – The People Behind The Big Ideas of Operations …
Shigeo Shingo was a Japanese industrial engineer who played a key role in assisting Toyota develop the Toyota Production System (TPS), a precursor to the highly popular Lean production system popular around the world today.