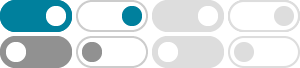
Cavitus BLE foam control system is an essential piece of equipment to increase production efficiency. The Generation II model has the latest developments in ultrasonic technology, improving the efficiency of the transducer. This enabled Cavitus to release a state of the art cool transducer that eliminates the
Cavitus Europe AG, Blegistrasse 9 Baar, 6340 Switzerland T: 41-412 www.cavitus.com [email protected] Distributors in: USA, South America, Central America, Africa, Russia, Mid-dle East, China, India, Austra-lia and Japan ound Tehnology- ound Investment ounds lie you should be taling to Cavitus Technical Data Sheet Gen2T (Self-cooled) FoamControl
Cavitus utilises patented technology to temporarily change the behaviour of feed stock in this process, to improve yield by up to 10%, enabling you to increase your throughput by 10% or reduce energy consumption by a similar magnitude. This effectively lowers your unit energy cost and reduces your overall fixed and variable
Solution : Cavitus fitted a Gen2 de-foaming unit to the line, rated to 75,000 bottles per hour. As this line had high foam levels and a speed of 42,000bphr the larger powered unit was recommended. The Cavitus unit was fitted 150cm prior to capper. The installa-tion of the transducer/sonotrode on the star wheel
Solution : Cavitus fitted a Gen2 de-foaming unit to the line, rated to 75,000 bottles per hour. As this line had high foam levels and a speed of 48,000bphr the larg-er powered unit was recommended. The Cavitus unit was fitted 150cm prior to capper. The installation of the transducer/sonotrode on the star wheel was com-
Solution : Cavitus fitted a Gen2 FoamControl unit to the line, rated to 120,000 cans per hour. As this line had high foam levels and a speed of 95,000cphr the larger powered unit was recommended. The Cavitus unit was fitted just before the last CO 2 bub-ble breaker and 40cm prior to the seamer entrance.
Result : By applying the Cavitus foam control sys-tem prior to jetting on the star wheel section of the filler, the benefits delivered to the customer were; 1. Increased filling speed from 34,000 to 40,000 bph 2. Reducing the foam loss around the jetter and capper section of the line, 3. Maintaining the same TPO level,
Solution : Cavitus fitted a Gen2 Foam Control unit to the line, rated to 120,000 cans per hour. As this line had high foam levels and a speed of 95,000cphr the larger powered unit was recommended. The Cavitus unit was fitted just before the last CO 2 bubble breaker and 40 cm prior to the seamer entrance. The installa-
Cavitus The Gen1 Converter and Sonotrode are designed and built from stainless steel and titanium to the highest standard in Switzerland. The unit is suitable for CSD lines to 24,000 units ph and Beer lines to 36,000 units ph. It is CIP and IP67. This unit is combined with a robust generator package and
Cavitus uses ultrasound technology to deliver productivity improvement on existing Beverage Filling Lines, whether carbonated soft drinks (CSDs), non-carbonated juices, teas, dairy drinks, sparkling wine, carbonated alcoholic pre-mixes or beer. The solution can be applied to can, bottle and pouch containers on CSD, aseptic and hot-fill lines.