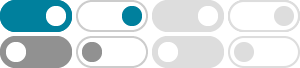
4M Analysis Examples and Description: Cause-Effect Diagram
Jul 28, 2022 · As we give you a little background to this Method, the idea of using the 4M is from Kaoro Ishikawa. The methods are an excellent intermediate that can help everyone analyze a …
Ishikawa diagram - Wikipedia
Ishikawa diagrams (also called fishbone diagrams, [1] herringbone diagrams, cause-and-effect diagrams) are causal diagrams created by Kaoru Ishikawa that show the potential causes of a …
What is a Fishbone Diagram? Ishikawa Diagram | Cause
Mar 20, 2020 · “Fishbone Diagram” also known as “Ishikawa diagram” and “Cause and Effect diagram. It helps to Identify all potential or probable causes and select the best cause which …
4M Analysis | Fishbone Diagram - INDUSTRIAL TRAINER
4M analysis is a problem-solving method that is used to identify and address the root cause of a problem or defect in a process. The 4Ms in the 4M analysis refer to Manpower, Machine, …
Ishikawa Diagram: How to Effectively Perform Root Cause Analysis
Kaizen methodology – where it is applied as 4M (Man, Machine, Method, Material) or 4M + 1D (Design) It’s an excellent tool for correctly identifying the root cause of a problem, which …
How the 4M Method Can Improve Your Manufacturing Operations
Sep 23, 2024 · Ishikawa wanted to determine how to apply continuous improvement to processes when all variables are known. The result was the fishbone diagram (initially composed of 6Ms) …
Fishbone Diagram, Types, Advantages, Drawbacks, and Six M’s
Oct 5, 2023 · Each type focuses on different aspects of the problem and helps to uncover a specific set of potential causes. A streamlined version of the Ishikawa diagram, known as the 4 …
4 Ms fishbone diagram - Production process | 4 Ms fishbone …
The 4Ms fishbone diagram (cause and effect diagram, Ishikawa diagram) example "Production process" was created using the ConceptDraw PRO diagramming and vector drawing software …
ISHIKAWA GUIDA PRATICA: Causa-Effetto, 4M e i 5 Perché
Il diagramma Ishikawa o diagramma causa effetto, è il metodo più diffuso per l'esecuzione della Root-Cause-Analysis. Impara come si fa!
Diagrama Causa-Efecto (Diagrama Ishikawa) - Progressa Lean
Sep 16, 2014 · Se trata de una herramienta para el análisis de los problemas que básicamente representa la relación entre un efecto (problema) y todas las posibles causas que lo …