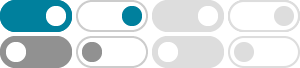
Unusual defects, generated by wafer sawing: An update, including …
Aug 1, 2015 · When doing a detaping (often also called “peeling”) step (Fig. 4), charge separation takes place with a high risk of ESDFOS (ESD from outside to surface), especially in front side detaping. Such damage may induce severe surface damage to top layer metallizations; Fig. 5 shows typical ESDFOS impacts.
Abstract— This paper describes the development of a robust process to improve chipping and peeling defect on low-k/heavy metalised saw street wafer during die singulation process using laser grooving technique.
Low-κ F-RAM wafers are more difficult to saw than standard silicon wafers. These wafers have a higher chance of metal and passivation peeling, top-side and bottom-side chip-outs, and sidewall cracks. Standard silicon wafer sawing processes not modified for low-κ wafers can result in excessive yield loss. Laser Grooving
Method for eliminating backside metal peeling during die …
A method of protecting metal traces and contacts on a fabricated semiconductor wafer from mechanical damage during dicing of the fabricated wafer, where the metal traces and contacts form...
Delamination, or peeling, is a common defect mode induced during conventional mechanical dicing of any wafer with Low-k technology of 65nm or below. As a result, a laser grooving step is typically introduced to create a shallow trench through the Low-k dielectric layer prior to a mechanical saw cutting through the remaining silicon material.
Initial DOE on the three identified risks at wafer sawing was conducted to validate OEM default parameters. The three identified risks are front side chippings or peeling, metal dangling, and passivation cracks. Effectiveness of laser grooving was
Mechanical wafer sawing is a cutting process in which dice from a wafer are singulated in individual unities. The area that is allowed to be cut during sawing process is called sawing street and the key factor to determine the quality of the process is to value the extent of chipping or peeling since the effect
300mm low k wafer dicing saw study - IEEE Xplore
Aug 30, 2005 · The introduction of low k material into silicon imposed challenges on dicing saw process, ILD and metal layers peeling and its penetration into the sealing ring of the die during dicing saw are the most common defects.
MTS - Wafer Saw
MTS Wafer Saw Cutting Speed/ UPH Solution – UPH Solution, improve > 50% WAFER SAW shows a lot of opportunities for improvements, from MTBA –Alarms like Kerf Check, MTBF -Machine down, Blade Setup, Auto dressing, Spinner Wash/ Dry.
ANALYSING BACKSIDE CHIPPING ISSUES OF THE DIE AT WAFER SAW
Jan 1, 2003 · Thinner wafers are more prone to cracks even before saw because of the stress management during the back grind process. This paper focuses mainly on backside chipping issues as a result of crack...
- Some results have been removed