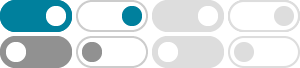
Rotor skew pattern design and optimisation for cogging torque reduction ...
Jun 1, 2016 · The rotor linear skew technique helps reduce the cogging torque and torque ripple for IPMSMs, but with non-negligible increase in the axial force. The three-, four-, and five-step herring-bone skew patterns lower the cogging torque, the torque ripple, and the axial force with slight influence on the average torque.
Skewing involves the deliberate angular displacement of stator or rotor laminations to break the symmetry and alter the magnetic field distribution, thereby reducing the cogging torque. One typical method for lowering torque ripple and cogging torque is rotor/stator skew design [7].
Four- and five-step symmetric skew, herring-bone skew, and five-step W-shaped skew patterns provide an adequate reduction in the cogging torque and axial force, but they have higher excitation torque ripple compared with the linear skew pattern.
Electric motor basics: Why are rotors skewed? - EASA
The purpose of the skew is to reduce harmonics in the air gap flux that are introduced by a certain stator-rotor slot combination. The rotor is more commonly skewed than the stator, because coil insertion becomes more difficult, and slot opening cross-section decreases, with skewed slots.
Usually, rotor slots are skewed in low- and medium-power induction motors to overcome the slot effects and especially pulsating torques. Skewing decreases the rotor's electromotive force harmonics. As a result, the harmonics of rotor currents and their relative losses are reduced, too.
create a single directional skew on the rotor, but in this study, a double-sided skew method is proposed as an alternative to the traditional skew method and the torque behavior of the motor is investigated. For this study, while the traditional skew method is applied as 5 degree, skew ratios of 5 and 10 degrees
Methods for calculation of skewed permanent magnet motors for …
Skewing of either the rotor or the stator stack is a widely applied method for reducing cogging torque and torque ripple in permanent magnet motors. The basic idea behind skewing is to influence the interaction between the rotor magnets and the stator slots.
A Methodology for Applying Skew in an Automotive Interior
Dec 15, 2023 · Skewing of the rotor or stator is a widely adopted method to minimize NVH. However, determining the optimal skew parameters is challenging and may result in suboptimal designs.
Optimizing PMSM Performance: Effects of Airgap Length and Skew …
Skewing involves arranging the laminations of the rotor or stator at an angle to the motor axis, reducing cogging torque and torque ripple and resulting in smoother and quieter motor operation. Different skew techniques are defined in the literature …
Linear rotor skew (left) and stator skew (right) of a PMSM
Fig. 7 shows a typical linear rotor and stator skewing used in traction motors. Airgap harmonics can also be reduced by geometric features on the rotor surface as well as with flux barriers...