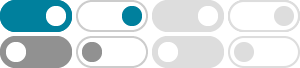
Exploring the Advantages of PVD Coatings for Knives
Jan 24, 2024 · By weighing the extended corrosion protection, scratch resistance, attractive colors, and sharp bonding against slightly higher costs and eventual reapplication needs, consumers can determine if PVD coatings provide worthwhile advantages for …
DLC and PVD coating durability - BladeForums.com
Dec 29, 2012 · The coating on any knife will wear over time, given it's used on enough abrasive material. It all depends on what you are cutting, dense/dry/seasoned hardwood will eat the coating faster than green/moist/non-hardwood.
How The Pros Coat Their Knife Blades - BLADE Magazine
Dec 23, 2011 · President and co-owner of Spartan Blades, Curtis Iovito said his company’s coating of knife blades is called Physical Vapor Deposition (PVD). “The process is characterized by the creation of a material vapor that can be reacted with different gases to form a thin film coating,” he noted.
DLC & PVD Knife Coating Machines - PVD Systems For Knives
Use PVD and DLC coatings on your knives and blades for less than $1 per part coating cost with one of our right-sized PVD/DLC coating machines. Over the past few years, PVD & DLC coatings have become a significant selling point for luxury goods, including high-quality knives.
The Most Popular Knife Blade Coatings | Red Label Abrasives
Also known as TiN coating, this hard ceramic powder is often used as a coating on titanium alloys, steel, carbide, and aluminum parts. Applied as a Physical Vapor Deposition (PVD), TiN is used for hardening and protecting cutting and sliding surfaces as well as providing nontoxic coatings for surgical devices.
The variety of blade finishes and why they are important - SMKW
PVD, or Physical Vapor Deposition, is a coating process used to apply thin films onto knife blades for improved performance and appearance. In PVD, a vaporized material is deposited onto the blade's surface in a vacuum environment.
What is PVD Coating? A Complete Guide to Physical Vapor …
PVD coating is all over the place in real life, from heavy-duty factory tools to your kitchen faucet, even the chips in your phone. This guide’s here to break down the PVD coating meaning for you, covering the basics, the nitty-gritty of how it’s done, and where it shows up.
Blade Coatings Explained: Their Advantages - BPS
PVD (Physical Vapor Deposition) A thin, high-performance coating that provides excellent corrosion resistance and cutting efficiency. PVD coatings are applied using a process called physical vapor deposition, which involves vaporizing a metal or ceramic material and then depositing it onto the blade’s surface.
Blade Coatings & Finishes - Kai USA
Diamond-Like Carbon (DLC) coatings lower friction, offer high wear resistance, and enhance hardness. The benefits of such a coating are obvious when it comes to knives. PVD stands for Physical Vapor Deposition. Specialized materials are vaporized via a vacuum process. Then the vaporized material is deposited as a thin layer on selected objects.
Blade Coating: What You Need to Know for Sourcing
May 14, 2024 · PVD, or Physical Vapor Deposition, is like a high-tech spray tan for your blade. It involves vaporizing a coating material in a vacuum chamber and then depositing it onto the blade’s surface at a molecular level. The result? An impossibly thin, even layer.