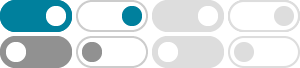
Lubricant Lifecycle Management - Part 1 - Machinery Lubrication
To ensure machine reliability, the offending lubricant requires maintenance actions that are properly designed and executed. This article discusses how oil degrades, proactive ways to extend the lubricant's life and proper disposal methods once the oil has been changed. Contrary to popular belief, oil doesn't last forever.
Predicting Oil and Grease Life - Machinery Lubrication
Oil content is a measure of remaining life and can be quantified in a grease sample by atomic absorption spectroscopy or by solvent separation and weighing of the remaining oil. Greases typically fail after losing about half their initial oil content.
This technical report defines the CFP for a lubricant product on a life cycle (Figure 1) or cradle-to-grave basis. Therefore, to generate the CFP, the absolute GHG emission and removals at each stage of the life cycle are
lube-oil’s life expectancy is under-standing how a lubricant degrades (Fig 1) and what tests are available to measure the amount of degrada-tion. Oxidation and/or heat are what cause Group 1, Group 2, and syn-thetics to degrade. Generally, oxidative degradation doubles for every 18-deg-F increase in lube-oil temperature. Group I oils
Conditions which may affect oil lubricant shelf life are as follows: Both high heat (greater than 110°F) and extreme cold (less than 0°F) can affect lubricant stability. Heat will increase the rate of oil oxidation. Cold can result in wax and possible sediment formation.
Normal Shelf Life: In general, the recommended shelf life for oils and greases is typically fi ve years when stored properly in the original sealed containers. Cloudy appearance or strong odor. Engine oils stored in UNSEALED containers for a prolonged period of time will absorb moisture from the air and may develop a hazy appearance.
Lubricant life cycle assessment comparisons - petroleum, bio-based, synthetic and re-refined lubricants 2 • Inventory of energy and material inputs and environmental releases
Abstract A general life cycle assessment (LCA) study of base oils used in the manufacture of lubricating fluid is given in this chapter. The scenarios of mineral oil, a synthetic ester, and a vegetable (rapeseed triglyceride oil) are investigated. The review of LCA leads to drawing conclusions concerning the application of
Lube-oil cleanliness critical to long bearing life
Lessons learned over the years point to these Top 10 ways contamination can kill your bearings: No. 10, Mixing lubricants. Most plants store their lubricants in one place.
Lubricant Lifecycle Management - Part 2 - Machinery Lubrication
By managing temperature, moisture, particles and other contaminants, the life of the lubricant can be proactively extended and oil analysis can provide the necessary information to make the oil change decision, assuming the application is a suitable candidate for condition-based drains.
- Some results have been removed