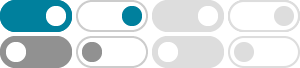
5S and 7S | Know Benefits Of Implementing and Practical Uses
Jan 23, 2023 · The 5S concepts are expanded upon by 7S, which places an emphasis on employee development and environmental awareness. 5S and 7S implementation improves workplace productivity, safety, quality, and overall effectiveness.
Dec 4, 2015 · The 7S implementation consists of seven phases shown in Figure 3 viz. Sort, Set in order, Shine, Standardize, Sustain or Self Discipline, Safety and Spirit. Each phase continuously improves the performance of an organization by eliminating wastages of searching,
McKinsey 7S Model - Overview, Structure and Application, Example
The McKinsey 7S Model refers to a tool that analyzes a company’s “organizational design.” The goal of the model is to depict how effectiveness can be achieved in an organization through the interactions of seven key elements – Structure, Strategy, Skill, …
McKinsey 7S Model: The 7S Framework Explained - SM Insight
Dec 3, 2023 · McKinsey 7S model is a tool that analyzes company’s organizational design by looking at 7 key internal elements: strategy, structure, systems, shared values, style, staff and skills, in order to identify if they are effectively aligned and allow the …
The McKinsey 7-S Model for Organizational Alignment and Success
Learn how leaders leverage the Mckinsey 7-S model - a strategic framework analyzing structure, strategy, systems, skills, staff, style and shared values - to diagnose gaps, guide transformations, and improve organizational effectiveness.
A Review on Seven S (7S) as a tool of Workplace Organization
Each phase continuously improves the performance of an organization by eliminating wastages of searching waiting, transportation, motion, work in progress inventory etc. 7S also makes the working environment clean anc safe that improves the morale of the employees.
Lean Manufacturing and the 7S Methodology - brighthubpm.com
Some businesses have expanded the 5S framework by adding two additional steps to create 7S: Spirit and Safety. The methodology is used in manufacturing as well as office settings, and is one of the most popular Lean tools.
7S management - qualitybook.org
Jun 27, 2023 · 7S management is an abbreviation for the seven words Seiri, Seiton, Seiso, Seikeetsu, Shitsuke, Safety and Speed/Saving. Because the first letter of these seven words in Japanese and English is “S”, it is referred to as “7S” for short.
5S, 6S and now 7S is a path to a safe, productive, and high-quality ...
5S, 6S, and now 7S is a system that aims to promote and sustain a high level of productivity, quality, and safety throughout a workspace. 5S, 6S, and now 7S, establish a universal set of workplace principals: Sort, Set in Order, Shine, Standardize, Sustain, Safety and Synergy. (We like the word synergy)
7S Lean Practices: The Key to Achieving Efficiency and ... - LinkedIn
Feb 15, 2023 · The 7S Lean Practices model is a proven methodology that helps businesses to achieve efficiency and productivity by streamlining their processes and eliminating waste.