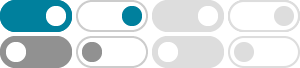
6S Method in Lean Six Sigma for Continuous Improvement
Mar 26, 2024 · The six key principles of the 6S methodology are: Sort (Seiri): Identifying and removing unnecessary items from the workplace, reducing clutter and potential hazards. Set in Order (Seiton): Organizing and labeling necessary items in a logical and accessible manner, ensuring efficient workflows.
What is 6S Lean? 5S + Safety: A Guide - SafetyCulture
Aug 17, 2024 · 6S in manufacturing is an approach to production that integrates the 5S principles (Sort, Set in order, Shine, Standardize, and Sustain) in manufacturing processes, with the additional factor of Safety. This method helps address critical manufacturing issues.
What is 6S in Manufacturing? The Meaning, Benefits & Tips
The fundamental process of the 6S, sorting, is specifically designed to find out all this information. You need to identify the items placed in the working area to decide what to do with them. Optimize the process by tagging the equipment with color tags or with inspections software.
What Is the 6S Method? (With Definition, Benefits and Tips)
Mar 3, 2025 · The first principle of the 6S method is sorting. The sort phase involves separating necessary items and supplies from things not used on a daily basis or properly stored. This phase makes it easier for teams to navigate their workspace safely and effectively.
5S vs. 6S – What’s the Difference? - Lean Workplace
Aug 2, 2023 · The 6S steps are: Sort, Set in Order, Shine, Safety, Standardize, and Sustain. By integrating safety as a core component, the 6S approach emphasizes the importance of identifying and mitigating potential hazards in the workplace.
What is 6S Lean? Improved 5S Methodology - Certainty Software
Jan 27, 2022 · 6S lean manufacturing combines the five key tenants of 5S — sort, straighten, shine, standardize, and sustain — with safety. The goal of 6S is to ensure that safety is a part of all lean manufacturing processes from end to end, in turn reducing the risk of accidents and limiting the amount of production downtime.
6S Method: Definition & Process - Operations1
The six steps of the 6S method are: Seiri (sort), Seiton (set in order), Seiso (shine), Seiketsu (standardize), Shitsuke (sustain), and Safety (safety). Seiri (Sort) Unnecessary tools and materials are identified and sorted out.
A Very Important Lean 101 Technique- 6S
In a nutshell, it is a cleaning and organizing method. The old saying “a place for everything and everything in its place” is key to 6S. Let’s go through the different S’s. 1. Sort. Just as it sounds, you go into an area and sort through everything in that area.
6S Method: Definition, Key Steps & Workplace Efficiency Tips
Seiri (Sort) – Identify and remove unnecessary tools and materials to create a clutter-free, organized workspace. This ensures that only essential items remain, improving efficiency. Seiton (Set in Order) – Arrange necessary tools and materials in a logical, easy-to-access manner.
6S Methodology: Meaning, Process, and Standards for Lean …
What is 6S Methodology? A key part of lean management is the 5S methodology, which is complemented by the 6S methodology. Sort, set in order, shine, standardize and sustain are the main components of 5S. A component called safety was added as the 6th S to the original model.