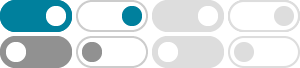
What is 6S Lean? 5S + Safety: A Guide - SafetyCulture
Aug 17, 2024 · 6S (otherwise known as 5S + Safety) is a system that aims to promote and sustain a high level of productivity and safety throughout a workspace.
6S Method in Lean Six Sigma for Continuous Improvement
Mar 26, 2024 · The six key principles of the 6S methodology are: Sort (Seiri): Identifying and removing unnecessary items from the workplace, reducing clutter and potential hazards. Set in Order (Seiton): Organizing and labeling necessary items in a logical and accessible manner, ensuring efficient workflows.
What is 6S Lean? Improved 5S Methodology - Certainty Software
Jan 27, 2022 · 6S lean manufacturing combines the five key tenants of 5S — sort, straighten, shine, standardize, and sustain — with safety. The goal of 6S is to ensure that safety is a part of all lean manufacturing processes from end to end, in turn reducing the risk of accidents and limiting the amount of production downtime.
What is 6S in Manufacturing? The Meaning, Benefits & Tips
The 6S helps to predict and schedule the maintenance of the tools, get rid of unused items, efficiently use components with closing shelf life (e.g., chemicals or batteries). This practice allows for investments, orders, and costs optimization.
Streamlining Efficiency with the 6S Lean Process: Sort (Seiri)
Sep 5, 2023 · In part one, we will explore the first step of the 6S Lean process, Sort (Seiri). Sort enhances efficiency, reduces waste, and creates a streamlined work environment. Organize and Tag Items. The Sort step is all about organizing and decluttering work spaces.
6S Method: Definition & Process - Operations1
The 6S method, also referred to as "5S + Safety", assists in maintaining productivity and safety in the workplace. The six steps of the 6S method are: sort, systematize, clean, standardize, self-discipline and safety.
What is 6S in Manufacturing? - paperekart.com
Sep 17, 2024 · The bottom line: 6S is a low-investment, high-impact lean manufacturing tool that centers on people. It engages operators in taking ownership of their workspace and helps instill a culture of quality, productivity, and continuous improvement.
What is 6S Lean? - Integrating Safety in the 5S Method
Jul 23, 2024 · The 6S method combines Sort, Set in Order, Shine, Standardize, Sustain, and Safety to enhance workplace organization and safety. It goes beyond arranging the physical space by fostering a culture of continuous improvement, accountability, and …
Feb 13, 2005 · What we call "6S" derives from "5S" the method of workplace organization and visual controls developed by Hiroyuki Hirano (5 Pillars of the Visual Workplace, Portland, OR: Productivity Press, 1990). The five "Ss" refer to five Japanese words—seiri, seiton, seiso, seiketsu, and shitsuke.
6S Methodology: Meaning, Process, and Standards for Lean …
6S Core Principles. The core principles of 6S are designed to simplify workflows and create a culture of continuous improvement, enhancing efficiency and organization: Sort (Seiri): Get rid of everything that’s not necessary. This step ensures only what’s needed is left, reduces distractions and minimizes hazards.