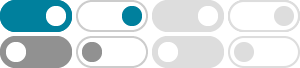
What is 6S Lean? 5S + Safety: A Guide - SafetyCulture
Aug 17, 2024 · 6S in manufacturing is an approach to production that integrates the 5S principles (Sort, Set in order, Shine, Standardize, and Sustain) in manufacturing processes, with the additional factor of Safety. This method helps address critical manufacturing issues.
6S Method in Lean Six Sigma for Continuous Improvement
Mar 26, 2024 · The 6S approach encourages the identification and elimination of waste, whether it’s unnecessary inventory, inefficient processes, or underutilized resources. By optimizing material handling and reducing waste, organizations can achieve significant cost savings.
What is 6S in Manufacturing? The Meaning, Benefits & Tips
The 6S helps to predict and schedule the maintenance of the tools, get rid of unused items, efficiently use components with closing shelf life (e.g., chemicals or batteries). This practice allows for investments, orders, and costs optimization.
What is 6S Lean? Improved 5S Methodology - Certainty Software
Jan 27, 2022 · 6S lean manufacturing combines the five key tenants of 5S — sort, straighten, shine, standardize, and sustain — with safety. The goal of 6S is to ensure that safety is a part of all lean manufacturing processes from end to end, in turn reducing the risk of accidents and limiting the amount of production downtime.
5S vs. 6S – What’s the Difference? - Lean Workplace
Aug 2, 2023 · The 6S steps are: Sort, Set in Order, Shine, Safety, Standardize, and Sustain. By integrating safety as a core component, the 6S approach emphasizes the importance of identifying and mitigating potential hazards in the workplace.
Achieve Workplace Excellence with the 6S Method
Nov 27, 2024 · The 6S method enhances workplace efficiency by promoting organization, cleanliness, standardization, perseverance, and safety. Originating from the Kaizen philosophy, it comprises six steps: Sort, Set in Order, Shine, Standardize, Sustain, and Safety.
6S Method: Definition & Process - Operations1
The 6S method, also referred to as "5S + Safety", assists in maintaining productivity and safety in the workplace. The six steps of the 6S method are: sort, systematize, clean, standardize, self-discipline and safety.
The Importance of 6S – 5s plus Safety | Crystal Lean Solutions
6S is a foundational element for Lean deployment and focuses on creating and maintaining an organised working environment. It helps businesses promote efficiency and establishes a sustainable culture of safety throughout a workplace.
Lean 6S; 5S + Safety - Lean Manufacturing Tools
5S is a methodical method to improve your housekeeping and standardize your processes making them more efficient and less stressful for your employees. 5S benefits are many, higher efficiencies, less stress, fewer accidents, higher levels of quality, fewer breakdowns and so on.
6S Methodology: Meaning, Process, and Standards for Lean …
☑️Learn what 6S methodology is and its role in lean manufacturing. ⭐Discover the meaning, process, and standards of 6S, including its focus on safety and workplace organization. Understand "what is 6S" and how it enhances efficiency and productivity. ⚡Optimize your manufacturing processes with the 6S system!