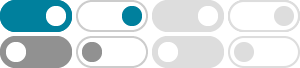
5S and 7S | Know Benefits Of Implementing and Practical Uses
Jan 23, 2023 · The 5S concepts are expanded upon by 7S, which places an emphasis on employee development and environmental awareness. 5S and 7S implementation improves …
5S, 6S, or 7S: Which Lean Approach is Best? - LinkedIn
Learn the differences and benefits of the 5S, 6S, and 7S methodologies, and how to apply them in your work environment to improve efficiency, quality, and safety.
Lean Manufacturing and the 7S Methodology - brighthubpm.com
The 5S methodology of Lean Manufacturing and Lean Six Sigma incorporates five different steps aimed at making the physical work environment as efficient as possible by eliminating …
5S - What are The Five S’s of Lean? | ASQ
Five S (5S) stands for sort, set in order, shine, standardize, and sustain. This method results in a workspace that is clean, uncluttered, safe, and well-organized, which can help reduce waste …
5S or 7S Lean Manufacturing and Workplace Organization – What …
5S and 7S are processes and methods for creating and maintaining an organized, clean, safe, and high performance workplace. Having a disorganized workplace will cost you time, money, …
5S, 6S and now 7S is a path to a safe, productive, and high-quality ...
5S, 6S, and now 7S is a system that aims to promote and sustain a high level of productivity, quality, and safety throughout a workspace. 5S, 6S, and now 7S, establish a universal set of …
McKinsey 7S Model: The 7S Framework Explained - SM Insight
Dec 3, 2023 · McKinsey 7S model is a tool that analyzes company’s organizational design by looking at 7 key internal elements: strategy, structure, systems, shared values, style, staff and …
5S (7S) – Japanese concept of workplace improvement
7S - SPIRIT - Transformation of the company culture - 7S is the basis of longterm improvement of company productivity at minimal cost, helps to eliminate waste and increase self-discipline. …
The Lean Greenhouse: From 5S to 6S to 7S!
Feb 22, 2008 · Based on this success, they expanded their 5S lean approach to include a 6th "S" for safety. The new 6S system includes a single event in the continuous improvement process …
From 5S To 7S: Towards Organizational Efficiency and …
The document discusses the evolution of the 5S methodology into a 7S system to improve organizational efficiency. 5S originated from Toyota's production system as a way to create …