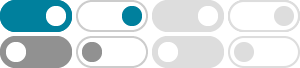
4M Analysis Process – Enhancing Your Business Performance
Aug 29, 2018 · The purpose of this procedure is to define the steps to do a 4M Analysis of a system or subsystem. The goal of this 4M Analysis Procedure is to reduce losses in the factory by using the Equipment Attributes as a guideline to achieve this end. Focused Improvement training can be taken here.
4M Analysis Examples and Description: Cause-Effect Diagram
Jul 28, 2022 · The 4M is a method to identify the cause behind the specific effects. The Method possesses four categories, and it is also what the name of the Method stands for– material, method, machine, and man. These categories are the elements that build the Method.
How the 4M Method Can Improve Your Manufacturing Operations
Sep 23, 2024 · The 4M Method is a way to identify and group the causes of a specific problem or effect in a manufacturing process. The four factors most manufacturers use are Manpower, Method, Material, and Machine.
Four Ms - Lean Enterprise Institute
1 day ago · In a lean system, the Four Ms mean: Material—no defects or shortages. Machine—no breakdowns, defects, or unplanned stoppages. Man—good work habits, necessary skills, punctuality, and no unscheduled absenteeism. Method—standardized processes, maintenance, and management.
4M Analysis | Fishbone Diagram - INDUSTRIAL TRAINER
4M analysis is a problem-solving method that is used to identify and address the root cause of a problem or defect in a process. The 4Ms in the 4M analysis refer to Manpower, Machine, Material, and Method.
The 4 Ms – the Determinants of Quality – Enhancing Your Business ...
Jan 2, 2022 · The key to ensuring quality (i.e. production standards) on the shop floor is achieving optimal conditions for the 4 Ms (Men/Women, Machinery, Materials, Methods), see Table “The 4-M Conditions – The Determinants of Quality”.
Eliminate Flaws in 4-M Conditions and Finalize
Jan 12, 2022 · Lean manufacturing aims to eliminate waste and improve the flow of materials and information throughout the production process. This approach is often used in manufacturing environments where efficiency and cost-effectiveness are critical, such as in the automotive and electronics industries.
4M’s of Operations Management | Milliken - Milliken & Company
Planned Maintenance: The 4M framework is instrumental in reducing breakdowns by restoring the equipment, correcting basic weaknesses, and preventing issues from coming back. Working together, 4Ms helps the pillars to understand where the weaknesses are and address them through restoration and prevention.
4M Analysis in Manufacturing: Boosting Operational Performance …
Applying the 4M rule isn’t just about improving isolated areas but understanding how these elements interact and contribute to overall efficiency. When done right, the 4M analysis becomes the cornerstone of a successful and agile manufacturing operation.
4M Principle - INDUSTRIAL TRAINER
The 4M principle provides a simple, yet comprehensive framework that enables managers to understand and manage the key factors that affect the performance of a process. By focusing on the four essential elements of Man, Machine, Material, and Method, managers can identify areas for improvement, prioritize changes, and implement effective ...